Read on to find out what makes HDF stand out from the rest of the construction materials.
Fiberboard consists of wood fibre (engineered wood) pressed with an adhesive resin binder under high heat and pressure. It is popular in the interior design market owing to reasons such as:
- It is versatile as it is available in various densities and thicknesses depending upon its usage.
- It is strong, which allows the manufacturers to maintain quality assurance & cost-effectiveness.
- It can be sanded/painted and easily drilled/cut as and when the need arises.
- It is lighter than solid wood and provides excellent acoustic performance.
A question often arises during the purchase decision process is whether to choose High Density Fiberboard (HDF) versus Medium Density Fiberboard (MDF). Here is a low-down on their properties to help you judge better:
HDF (High-Density Fiberboard) Material Properties
- It has a smooth surface and is resistant to fluctuations in humidity & temperature.
- It has a uniform density, higher strength and resilience than particle board.
- It is cheaper than solid wood but has no natural wood grain aesthetic.
- It can be used for structural elements like wall panels, furniture, flooring, shelves and cabinets.
- It is moisture-resistant but not waterproof, so it should be ‘sealed’ to combat water damage.
- It can be utilised mainly in the kitchen, living/dining area and bedrooms.
- It is highly durable, impact-resistant, flexible and environment-friendly.
- It has another upgraded version – High-definition HDF.
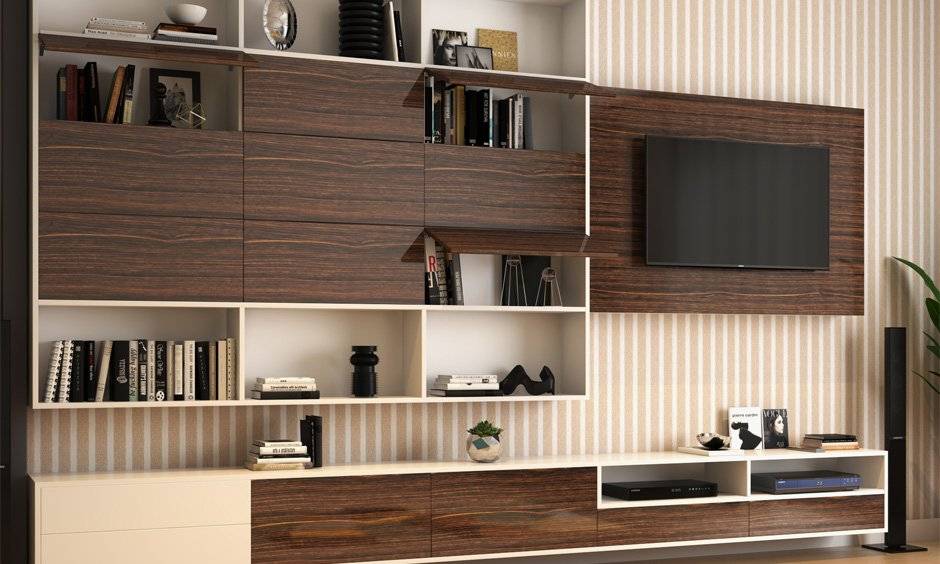
Medium-Density Fiberboard Properties
- It is less dense than an HDF board, making it easier to shape, cut, drill, paint, plane and seal.
- It has low water & humidity resistance but can be moisture-resistant with suitable edging.
- It is not as hard as HDF but has another upgraded version – High-definition MDF.
- It swells and warps less than a particle board and is very sustainable.
- It can be used for comparatively lighter and more decorative purposes like cornices, mouldings and grooves.
- It is much more affordable than HDF wood but available in multiple thicknesses.
- It is considered safe due to its low level of volatile organic compounds (VOCs).
- It is available in different types – Elite MDF, Standard Grade MDF, Exterior Grade MDF, Interior Grade MDF, Ultralite MDF, Prelam MDF and Melamine MDF.
HYDMR Properties
A third variety in engineered wood products has gained prominence due to its improved moisture resistance properties, making it eligible for use in high-moisture areas – HYDMR (Hydro-Density High Moisture Resistance) Boards. It has excellent dimensional stability. While MDF provides a consistent base for different design styles and HDF is often used as a substrate for veneer and laminate finishes, HYDMR can be used for both purposes. It can be machined similarly to HDF and MDF, although it will require appropriate techniques/tools because of its higher density and enhanced durability.
Safety Concerns Regarding MDF & HDF Materials
When working with HDF, MDF and HYDMR boards, one must observe a few associated safety precautions. The primary concern is the exposure to urea-formaldehyde (UF) gas emitted from the fiberboard products during their manufacture (more strength = more resin glue = more formaldehyde) and released many years after their use. Prolonged exposure to UF gas and wood dust can result in weakened eyes, sinus cancer, skin allergy, wheezing & coughing, ENT burning/bleeding sensations and more. Official health departments advise some best practices to reduce the exposure to wood dust and formaldehyde or lower the amount added to the UF resin of the fiberboard panels. Here’s how:
- Ensure proper ventilation in the installation area to extract the gases and dust promptly.
- Use a safer product like solid wood or composite panels with low or no added formaldehyde and keep the dust levels down with good housekeeping.
- Utilise alternate glues in the UF resin-like phenol formaldehyde, melamine formaldehyde (~less emission) and methylene diisocyanate, polyvinyl acetate, and soy (~no emission)
Cleanliness and Maintenance of HDF Board Laminate Flooring
- Sweep the floors with a soft-bristle broom and a less wet mop to remove the dust.
- Treat the spills immediately using a damp microfiber towel and a nail polish remover.
- Don’t slide heavy objects directly on the floor. Instead, use protective mats or wheels under the furniture.
- Use vinegar or oil-based cleaners available in the market or a properly formulated HDF laminate floor cleaner.
All in all, MDF or HDF sheets enhance the aesthetic appeal of your house while being affordable and versatile in their designs and usage. Book a free virtual consultation with the interior designers at DesignCafe if you want to have any more of your queries answered. We’d be more than happy to help.
Explore, More About
FAQs on HDF
1. Can HDF be used for structural applications, or is it mainly for decorative purposes?
Depending upon your specific needs, HDF can be used for structural or decorative purposes. It can be used for shelving, cabinets, bathroom vanities, flush panel doors, furniture pieces, decorative accents (baseboards & trims), wall panelling and more.
2. Can HDF be customised with various finishes, paints and patterns for different design styles?
Yes, absolutely. HDF wood can be personalised to represent different design styles using patterns, prints, paints, or finishes. Here are some of them:
· Print (floral, geometric, etc.)
· Textures (oak, mahogany, etc.)
· Paints (water-based, latex-based, acrylic, oil-based, etc.)
· Finishes (polyester or melamine coating, high-gloss, semi-gloss, matte finish, etc.)
3. How is HDFwood manufactured?
- The wood fibres are prepared by obtaining wood chips/ shavings and composing them into smaller pieces.
- The wood fibres are assembled in the mixing machine with the adhesive resin to bond strongly during the mixing/persistent stage.
- The wood fibres are then transformed into the desired panel shapes in a hydraulic press, wherein pressure and heat are applied to make a dense HDF panel.
- The HDF panel is made to cool down for a while to ensure the particles are firmly bonded, and the extra heat dissipates. Lastly, the other procedures like sanding, laminating and painting are carried out.
- 4. How to gauge the sustainability of HDF panels?
To understand the sustainability of HDF panels, one must gauge their life process using the life cycle assessment (LCA) method. This method facilitates thorough research and strategic creation of more sustainable products. Here is an overview of the lifecycle stages of HDF panels and each stage’s sustainability:
- Sourcing – It can be made sustainable owing to the utilisation of shavings/chips in sawmills and the carbon sequestration of the timber trees.
- Manufacturing – It can have a substantial carbon footprint due to the energy needed to run the machinery to process the wood waste and make the resin.
- Transporting is another carbon-intensive stage due to the emissions associated with hauling vehicles, from taking timber to sawmills, delivering wood waste to HDF factories, and bringing HDF furniture to the stores.
- Usage – The HDF furniture usage is made sustainable owing to the carbon capture during the products’ long life.
- End-of-life – The HDF furniture/panels are non-biodegradable but can be recycled.